What does a one-day transcritical CO₂ training course involve? Nick Johns-Wickberg headed out to Airefrig in Melbourne’s west to find out.
As high-GWP refrigerants are phased down and eventually out, carbon dioxide (CO₂) is one of several natural refrigerants that will continue to increase in popularity over the coming decade or so. Supermarket chains are leading the charge, with Woolworths recently announcing the launch of its 100th transcritical CO₂ store.
But despite the technology becoming more mainstream, there remains a significant skills gap. Many fridgies have never worked on transcritical CO₂ or received training about how it differs from classic refrigeration.
To remedy this, GOTAFE, CA Group Services, and Airefrig have collaborated to offer an accredited transcritical CO₂ training course supported by AIRAH, TAFE Victoria, and Bendigo TAFE. The course uses two mobile training pods that simulate the kind of transcritical CO₂ system you’d find in a supermarket.
The latest iteration of the training – which was predominantly for Woolworths refrigeration technicians – took place in five one-day sessions over the week of April 15–19 at Airefrig’s Truganina branch in Melbourne’s western suburbs. During the week, 62 fridgies attended and successfully completed the training.
I attended one of these sessions to speak with the instructors, meet the trainees, and see what’s involved in the training.
The classroom
We begin our day at 9am in the classroom, where instructor Peter McQueen gives trainees a one-hour recap of the theory behind transcritical CO₂ systems. A few weeks earlier, the trainees attended two four-hour Zoom sessions, in which McQueen went through the theory in detail. They then completed an online assessment through GOTAFE.
“They’ve turned up here with the theory covered and the theory assessment ticked off,” McQueen says. “It covers two units of competency: ‘Apply safety awareness and legal requirements for carbon dioxide refrigeration’ and ‘Repair and service carbon dioxide refrigeration systems’.”
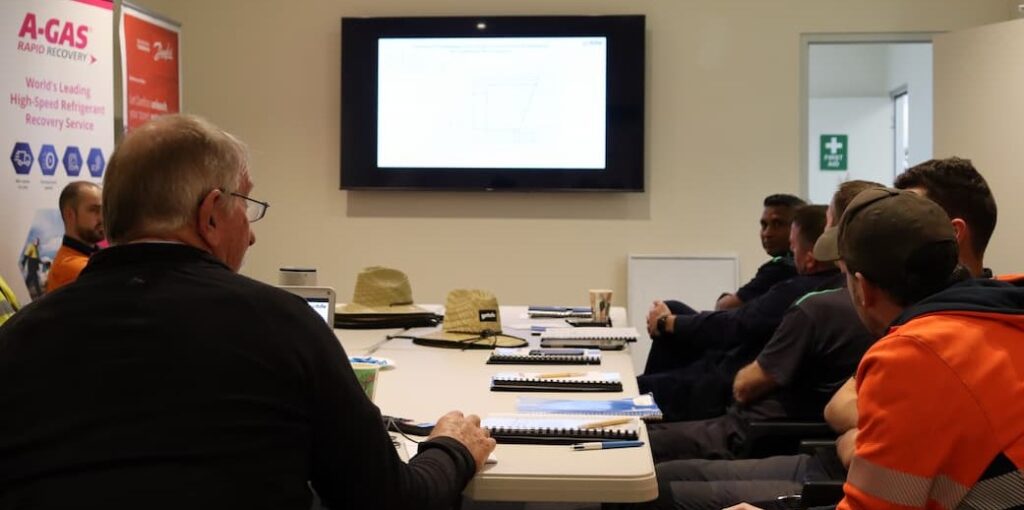
This classroom time is mainly for the sake of revision. However, it also gives trainees the chance to ask questions of the experienced instructors, who acknowledge that theory isn’t everyone’s strong suit.
“We learn best by doing things,” McQueen says. “Some of the guys do struggle a bit online.”
To pass their theory test, trainees have to achieve 100 per cent. They get several attempts to do this.
Hands-on training
Around 10am, we head outside and the real work begins.
The trainees today are from Woolsorths – some have travelled from country Victoria to be here, others from interstate. Scott Milburn, Assistant State FM Manager for Victoria and Tasmania at Woolworths, points out how serious Woolworths is about training its staff to work on these systems.
“Woolworths enrolled 61 technicians with a range of skill levels, so trying to ensure training meets the brief to support all levels was always high on our priority list,” Milburn says.
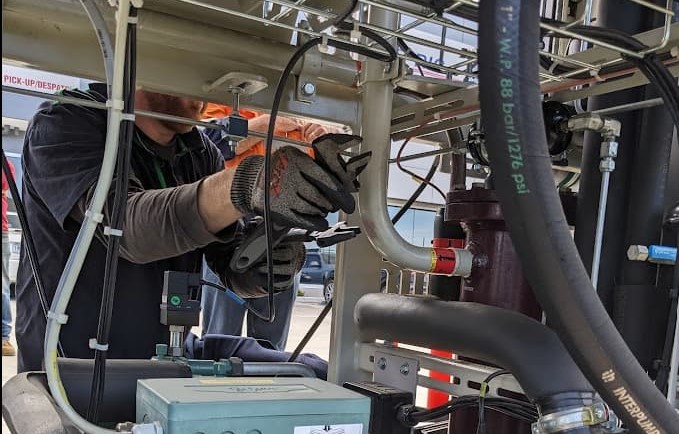
After a quick briefing from McQueen’s colleague, GOTAFE instructor Dave Smalldon, Affil.AIRAH, the trainees split into two groups of six, with each group working on one of the mobile training pods. During this time, McQueen and Smalldon encourage the trainees to explore the system and familiarise themselves with its components.
“After we’ve talked about the theory and those extra components that are unique to transcritical CO₂, we get them to come out here and just spend some time,” McQueen says. “It’s not even about running the plant; we just want them to open the doors up, follow the pipework, get a bit of paper and draw a mud map of where the components are, and get their head around it.
“A lot of what we do is observation. We use our senses; we look, we touch, we go around and look for patches of oil that might indicate leaks.”
McQueen and Smalldon are on hand to help the trainees with any questions and guide them as they navigate their way around the system. Once the trainees have familiarised themselves with the gear, it’s time to practise what they’ll later be asked to do in their assessment.
“There are two practical exercises we make them do,” McQueen says. “The first is to charge some refrigerant into the system, which they do in pairs. That involves setting up the equipment, bringing it down, using a bit of workplace health and safety – they use their head, not their back. They set it all up, charge some refrigerant, then shut it down and remove all the equipment.
“In the second exercise, they change an oil filter. This involves isolating some components and removing and replacing the filter.”
A spanner in the works
Maintenance and repair is rarely a smooth ride. Any number of faults could emerge, and fridgies need to be able to think on their feet to resolve potentially complex and evolving problems.
That’s why during the training, the instructors mix it up and put trainees to work in scenarios similar to what they might find in their everyday job.
“After they’ve had a good look at the system, I show them some scenarios where I actually force the system into some faults,” McQueen says. “I force it to run in subcritical, then we observe and discover things they can do on their plant at work. By opening valves, they can get some feedback on what does what. Then I trick it and force it to run in transcritical, regardless of the conditions, so they can see what changes.
“At a certain point I might throw it into overload and the whole thing shuts down, so they can see what’s going on.”

While these exercises are designed to challenge the trainees and make them think, they’re not trying to catch anyone out. McQueen and Smalldon supervise, instruct, and intervene where necessary.
Practical assessment
After lunch is when things get serious. The trainees must complete the two practical assessments: charging refrigerant into the system and changing an oil filter.
One of the benefits of this set-up is that there are two mobile training pods, each with their own quirks, as the trainees are likely to find when they move from store to store in their regular work. During the session, trainees need to perform the assessment tasks on both pods.
“To prove competency, they have to do it twice,” McQueen says. “The second time, they’ll go to the second pod, which is a little bit different – it’s got some different components.
“They’re getting true exposure to what they’re going to do, which is unique because a lot of TAFEs don’t have two different systems.
“When you train someone, you show them and do it together first, then they do it on their own.”
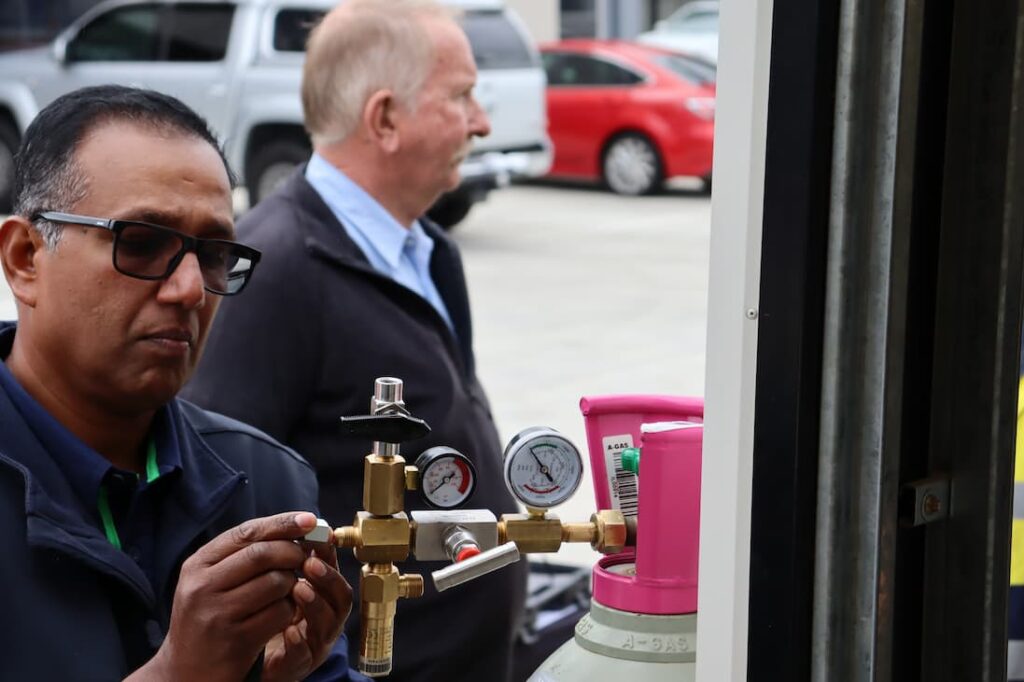
The response
During the training day, I chatted with several of the fridgies as they went about their work. They were full of praise for the trainers and the structure of the course, especially the practical components. They also felt that the knowledge they acquired during the session would be directly applicable to their everyday work.
Smalldon says this is typical of the broader response to the training.
“From every student and all the supervisors, the feedback has been nothing short of fantastic,” Smalldon says.
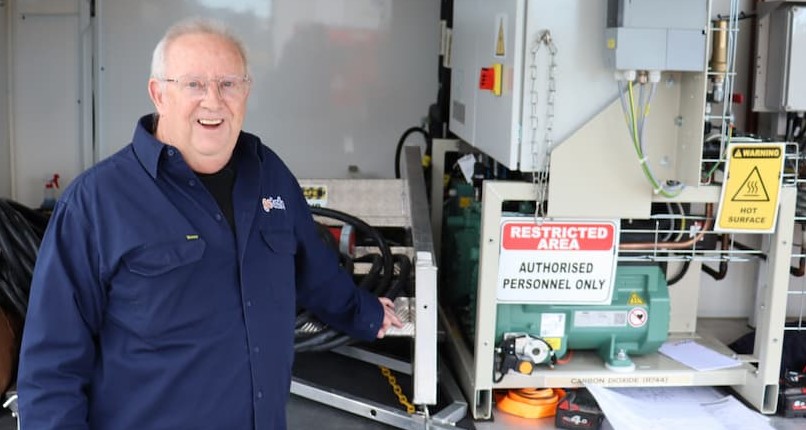
Scott Milburn from Woolworths describes the training as a success story for collaboration within the industry. He says feedback from technicians who have undertaken the course “has been extremely positive – engaging, hands-on, trade-relevant and safety-focused are some of the key callouts.”
The value of certification
An important feature of the training is that it’s certified. After their theoretical assessment and their day of hands-on training, participants come away with two formal competencies: ‘Apply safety awareness and legal requirements for carbon dioxide refrigeration’ and ‘Repair and service carbon dioxide refrigeration systems’.
Smalldon points out that not only are these qualifications useful, but they could soon become essential.
“In the future, it is anticipated that a licence or endorsement for CO₂ will happen,” he says. “The requirement will include these units.”
Milburn agrees, noting that formal certification is important for ensuring the quality of the company’s operations.
“One of Woolworths’ core values is ‘we’re always improving’,” Milburn says. “Certified training really enables Woolworths to deliver on our core values, improving technicians’ confidence and capabilities to deliver a high service standard to our primary customer: the stores.
“Relevant industry training for our team is a key component to supporting the upskilling of our team for now. However, the business will continue to see the return on investment as the knowledge cascades down to our 42 apprentices nationally over time. The industry is changing at pace, and the certified CO₂ course ensures our technicians have the correct accreditation for any class change moving into the future.”
What’s next?
Milburn says Woolworths plans to expand the training to ensure all its refrigeration mechanics are formally certified in CO₂ refrigeration.
“Woolworths will continue to invest in upskilling the entire team over time,” he says. “The initial training has been targeted to states that have a larger number of operational CO₂ and TCO₂ plants.
According to Smalldon, formal CO₂ regulation can’t come quickly enough.
“I am absolutely positive that training on transcritical and subcritical CO₂ systems should be mandatory and regulated,” Smalldon says, “due to the very high pressures and differences compared to other vapour compression systems.”
While providing CO₂ training to Australian fridgies en masse will be a challenge, the success of this course shows that the HVAC&R industry can rise to the occasion.
Leave a Reply